6V6 Trainwreck Express in recycled combo cabinet
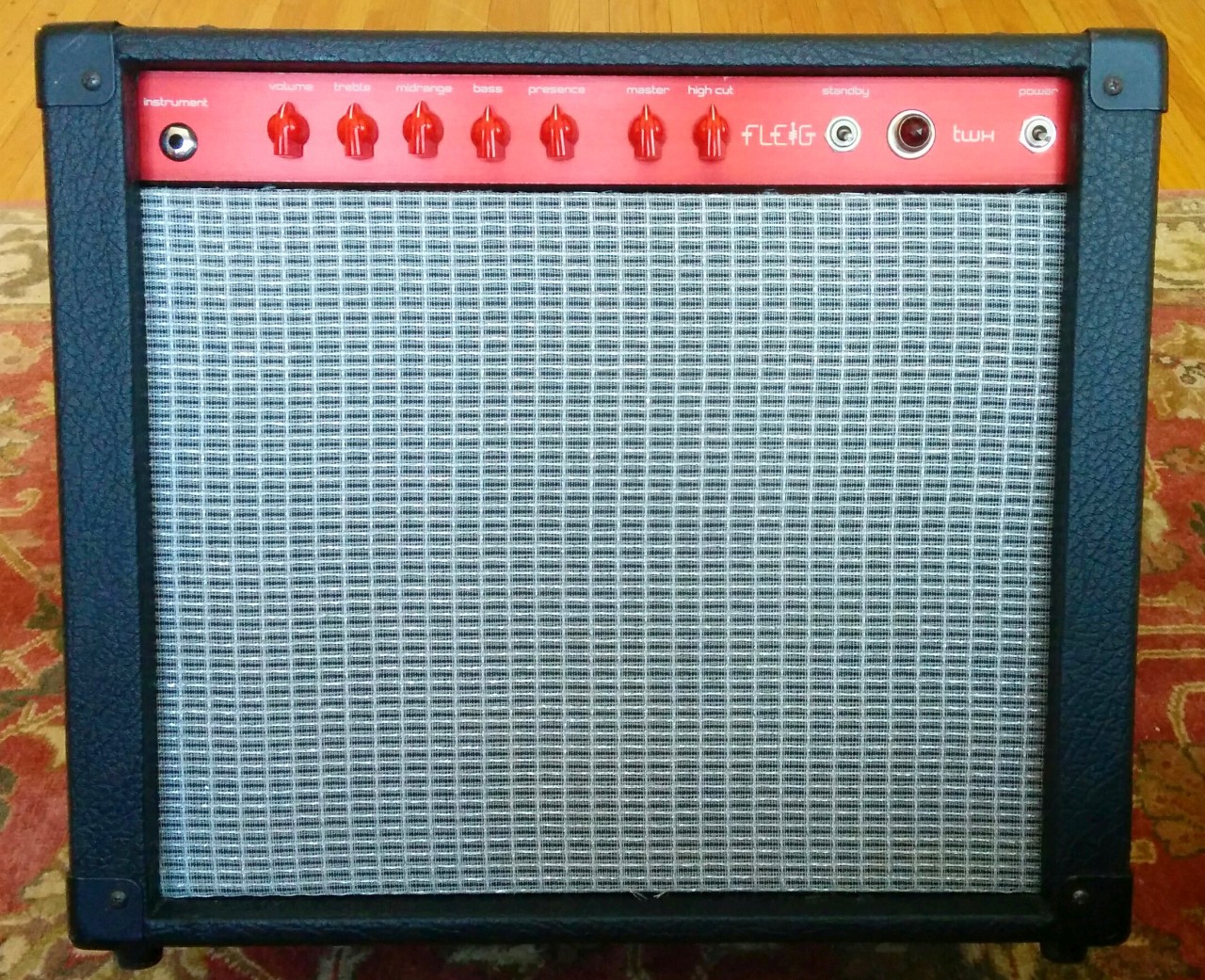 |
Evolution of an inexpensive solid state practice guitar
amplifier into a legendary Trainwreck Express
In 2009, my friend and co-worker Gary gave me his old solid
state guitar practice amp, a Peavey Envoy 110. It had
been sitting in a closet, and he wasn't sure it even
worked. I really didn't care if it worked, as I just
wanted a junk chassis and cabinet suitable for tube amp
hacking. I
ripped out its solid state guts, replacing them with a
vacuum tube circuit with a pentode preamp and cathode-biased
push-pull 6V6 output tubes. In January 2015, I began
the next step in its evolution, replacing the tube circuit
with my own take on Ken Fisher's Trainwreck Express design.
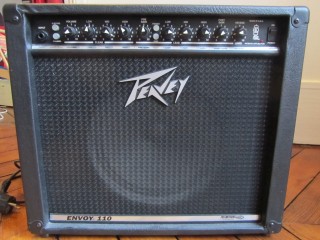
|
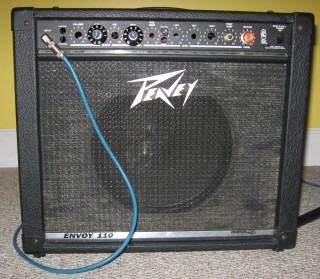
|
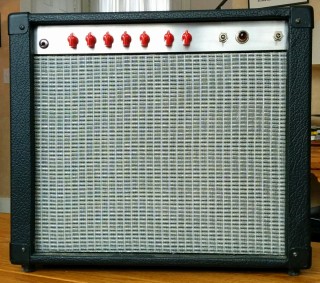
|
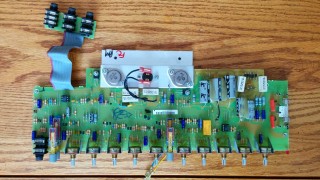
|
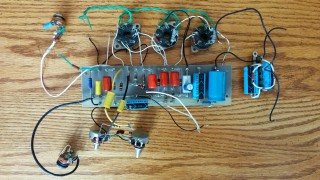
|
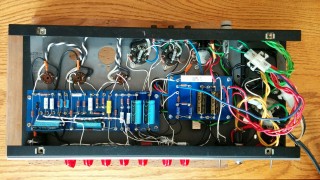 |
The amp as it came from the factory
around 1998 or so. Peavey does ok with the
Tolex job, but it's covering cheap MDF.Below is the
original solid state circuit board
|
As it appeared after I performed the
first conversion to tubes in 2009.
Since this was my hacking platform, I didn't spend
any time making it look nice. The circuit board is
my Moonlight prototype, now back on the shelf.
|
As it appears in its current
incarnation, before the front panel
was anodized and labeled. I actually made
baffle board and grill cloth (Fender blackface)
shortly after my first conversion.
|
|
Research and planning
I have never owned or built a high gain tube guitar amp, but
for quite a while I've have been curious about the mojo
surrounding the work of the late Ken Fisher.
Between the mid 80's and mid 90's, Ken produced about 100 of
his trademark Trainwreck Circuits amplifiers in several
models. Each amplifier is identified by a woman's
name, rather than a serial number. Reputation and
scarcity have taken the resale price of his original works
beyond $10,000 His amplifiers have long attracted the
interest of DIY builders. Starting around 1990, hand-drawn
schematics started appearing on the internet, supposedly
derived from examination of the guts of original
specimens. Several boutique builders have sold their
own versions of Fisher's designs, perhaps much as Jim
Marshall got into business making copies of Leo Fender's
1959 Bassman. I won't comment on the ethics or
politics of stealing/copying/borrowing in the guitar amp
business, but it's a sure thing that it happens a lot, for
better and for worse.
The special character of the Trainwreck is that the player
can take it from sparkly clean to ripping distortion using
only the guitar volume pot for basic control.
Fisher's work has spawned a kind of religion, where
disciples have documented every aspect of the design and
construction of his holy artifacts. In the
fundamentalist branch of this religion, it is seen as
desirable and necessary to the Trainwreck sound to use the
same layout, electronic components, chassis, and cabinet
materials used in Fisher's originals. Other adherents
believe that Ken's genius lies more in his deep
understanding of how to make great guitar amps from standard
parts, and that his legacy is better served by developing
one's own understanding, rather than by slavishly cloning
his artifacts.
I'm not religious about amp building, but I think more hope
for enlightenment lies in the second direction. The ampgarage.com forum
seemed to be the spiritual center for the study and
discussion of all things Trainwreck, so it was there I found
the scriptures on how to build one's own holy
amplifier. You have to register with the forum to view
attachments to posts. I could easily have built mine using
the traditional layout, but I wouldn't have learned very
much. Since I have built all of my projects from my
own layout, I chose to build the Express with my own board
layout as well. That way I'll find out if my methods
give quiet and stable results for higher gain circuits.
Fisher was reportedly quite forthcoming about his design
philosophy, and shared many of his insights in writings, and
conversations with other builders. I haven't studied
these much, but I think I understand enough about his
general practice to feel confident proceeding as I did.
Original Trainwrecks do not include a master volume.
To enjoy a Trainwreck at a volume that won't result in
hearing and/or structural damage, the standard solution is
to use an output attenuator. Fisher designed a
resistive attenuator that many have found quite
satisfactory. Many DIY builders have incorporated
master volume controls. The Lar-Mar
post-phase-inverter master volume circuit (PPIMV) , named
after its creators, seems pretty popular. A high-cut
control attached to the master volume is another popular
addition for taming the harsh high frequencies that can come
through when playing distorted, especially with the master
volume turned down. My build includes both the Lar-Mar
PPIMV and the high cut control.
To minimize the construction costs of my first Trainwreck, I
built my Express using an existing combo cabinet, speaker,
chassis, and transformer set. My belief is that the
critical factors in the success of a design rely much more
on the first-order properties of the circuit, i.e. its gain
structure, topology, operating points, and good construction
practice than on particular brands and models of electronic
components. That said, I do believe that transformers
matter a lot, and I was prepared to accept that my use of
semi-random power and output transformers might not result
in the sonic nirvana promised by using the blessed
components.
I borrowed a few layout details from Rick Norman, aka Dr. Vintage.
There is a Trainwreck Express build page on his website that
does not appear to be accessible through his index.
The page says not to link to it without written permission,
so I'm honoring that request. It is easy enough
to find with a search engine. One of his changes that
I used moves the unused triode section to V1, rather than
V2, to allow tube substitution to adjust the gain structure
in a more useful way. My particular interest was using
the second triode section in V1 to parallel the first gain
stage, as in some Matchless amps. For now I'm leaving
it unused to see how the standard arrangement sounds.
Because Ken Fisher's amplifiers have been intensively
documented, studied, discussed, and DIY built by many
others, I am not representing that my documentation should
be worthy of inclusion in the holy scripture of
Trainwreck. My original contribution is a new circuit
board layout that worked well for me, and that may be of
value to other DIY builders.
|
Circuit board layout
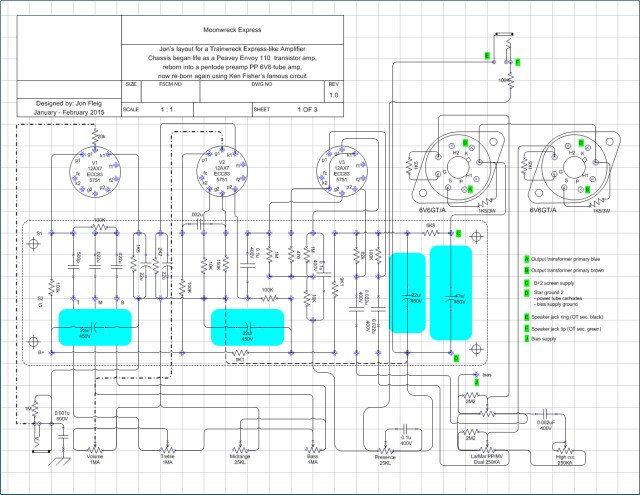
|
My first exercise for this project
was figuring out if I could lay out the main circuit
board on a leftover 8" x 3.125" piece of 1/8" thick
G10-FR4 board. I succeeded using my
traditional layout rules, which more or less follows
Doug Hoffman's
style.
After that, I laid out the power supply (HV
rectifier, reservoir caps, and bias supply) on
another 4" long leftover scrap of board.
My preferred style places filter capacitors on the
main circuit board close to the section each
serves. The negative lead goes right to the
cathode grounds. There is only one jumper
under the board, connecting the preamp stage ground
buss to the phase inverter ground.
There is only one connection from the chassis to
signal ground: the HV center tap, filament center
tap, and reservoir cap ground are attached to ring
terminals and screwed to the chassis near the power
transformer.
I do not tie my signal ground to the potentiometer
bodies, nor do I use a separate off-board ground
buss wire. Ground connections from pots and
jacks are made by directly wiring the control's
terminal to the cathode ground point of the
appropriate stage on the main circuit board.
To keep radio frequency interference from coming in
at the input jack, a 0.001 uF ceramic capacitor
connects the ground of the isolated input jack
(CliffUK) to the chassis.
I also found it necessary to mount a stopper
resistor (20k) on the first gain stage grid pin to
kill RF coming in with the guitar signal. I
didn't try any other value, so I can't say I know
the minimum value needed to perform this function.
I've mounted the output tube grid and screen
resistors on pins 1 and 6 of the octal
sockets. These are unused on 6V6's (and
6L6's). If you want to use my layout with
EL34's, these pins connect inside the tube, so
you'll have to mount these resistors somewhere else.
|
Power supply
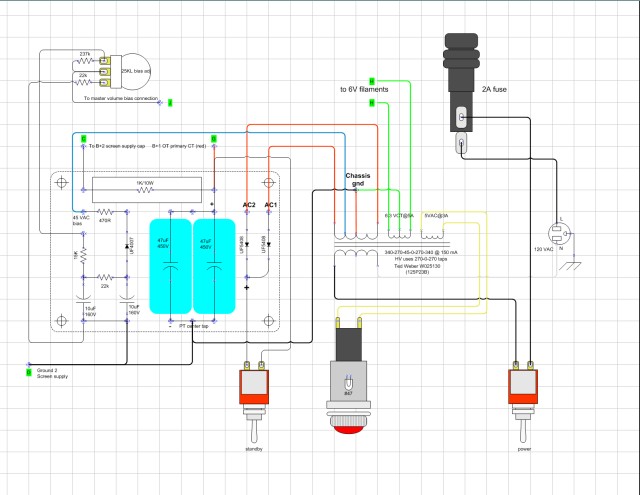
|
The Trainwreck Express wants a stiff
power supply. Fisher used a high current
capacity power transformer, solid state diode
rectifiers, and high reservoir capacitance.
However, he ran the tubes with lower B+ voltages
than Fender or Marshall favored, and biased the
power tubes for relatively low to moderate plate
current. Canonically, the Express uses EL34
output tubes, but Fisher designed it to be able to
use 6V6 output tubes just by re-biasing. My PT
and OT were designed to drive a pair of 6V6's.
With various rectifier options and high and low
voltage taps, my PT can supply anything from Fender
Tweed to Blackface sorts of voltages and
currents. The "official" Express PT has a
300-0-300 HV winding, and no separate bias
tap. Its standard B+ at the reservoir cap is
about 400 VDC at 300 mA. My existing
power transformer from Ted Weber has
340-270-0-270-340 windings with a 45V bias
tap. With full wave diode rectifier, the
270-0-270 winding predicted a B+ of 375 VDC at 150
mA, which is just fine for 6V6's. My
transformer's 340-0-340 taps are useful for amps
like the Fender Deluxe Reverb that use tube
rectifiers and run the output tubes at high
voltages, but this is way too high for
Trainwreck-like applications.
The rectifier diodes are usually specified as 2 x
1N4007 (1000 PIV / 1A) in series for each leg.
I used a single UF5408 (1000 PIV / 3A) for each leg
of the full wave rectifier. This may not have
been a good choice. A few days ago, one of my
UF5408 diodes shorted out, blowing the mains
fuse. I replaced both diodes. If it
happens again, I will use 2 x UF4007's in series, as
this doubles the peak reverse voltage capacity.
I used 2 x 47 uF @ 450V filter capacitors in
parallel for the main reservoir filter
capacitor. I can use caps rated for 450 VDC
here because I am using the lower voltage HV taps on
the power transformer (540 VAC).
The standard dropping resistor between the reservoir
capacitor and the screen filter capacitor is 1000
ohms @ 25 watts. Since this resistor only
carries the current for the output tube screens and
preamp plates, the total current passing through
this resistor is 6 mA at idle, and maybe 12 mA at
full power. This gives a power dissipation in
the resistor of I * I * R = 0.012A * 0.012A * 1000
Ohms = 0.15W. A 25 Watt resistor here seems to
be pure overkill. I substituted a 1000 ohm 10W
cement resistor.
Update: Why a 25W screen supply resistor is not
overkill
Many other builders beside me came to the conclusion
that a 25W resistor was overkill when the idle
dissipation at this node is less than one
watt. However, when an EL34 is driven near or
above its zero bias point, screen current increases
very rapidly. This probably applies to beam
power tubes such as the 6V6 as well. This
issue is discussed periodically on Ampgarage
and EL34World,
and the arguments for why Fisher used a 25W resistor
here seem solid enough to recommend sticking with
that value.
Since I'm only going to use 6V6's, and will probably
crank it up rarely, I feel OK leaving the 10W
resistor in there. However, I will probably
use a 25W resistor here in future builds.
The standard dropping resistor between the screen
filter cap and the phase inverter filter is
18.2K. Since my B+ is ~370V rather than ~400V,
I lowered this value to 6.8K to bring the remainder
of the preamp voltages up to the normal Express
values.
The bias supply differs slightly from the standard
version. Because my PT has a 45 VAC bias tap,
I don't have to use a large resistor off the HV
winding to obtain the bias voltage. I looked
at the AA763 Fender Deluxe Reverb to see what series
resistance was used between the bias tap and the
rectifier diode: 470 ohms. I used a 25K linear
pot for the bias adjustment, and with a 15K
fixed resistor above the pot, and a 22K resistor
below the pot to give me a bias range of about -16
to -35 VDC. A 237K resistor connects the bias
pot wiper to the bias voltage, to prevent a no-bias
condition if the pot fails.
I used the otherwise unneeded 5V rectifier winding
to power the pilot lamp.
|
Chassis layout
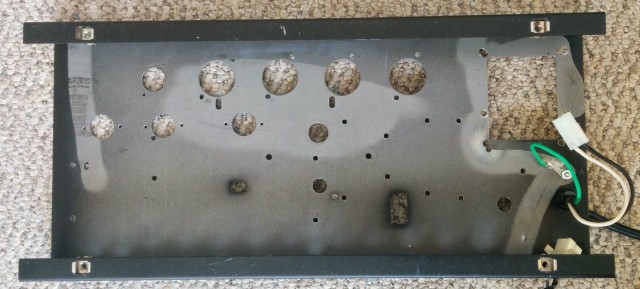
|
The chassis is recycled from two
previous builds: the way it left the factory, and
the first conversion from solid state to vacuum
tube. Thus, the chassis and control layout had
to be adapted to the existing holes. The
removal of the octal rectifier and phase inverter
tubes left two empty octal socket holes. To
keep the wires from the board to preamp tube sockets
short, I drilled new holes for 3 miniature tube
sockets, leaving the original preamp tube socket
hole empty. My friend Arpad made covers for
the unused octal socket holes from scrap
aluminum. I installed the bias pot in the
cover for the former rectifier tube socket. I
may eventually make beauty covers for the surplus
miniature tube socket hole and rear panel control
holes.
Neither the power transformer nor the output
transformer are mounted in the traditional locations
for original Trainwrecks. I simply retained
the power and output transformer locations from my
previous build in this chassis, because I already
knew that the OT did not pick up hum in its current
location and orientation. Since this is a
steel chassis that couples magnetic flux from
transformers, and not the aluminum preferred by
Fisher, I saw no reason to risk moving it to obtain
the traditional layout.
|
Fabricating the main and power supply circuit boards
|
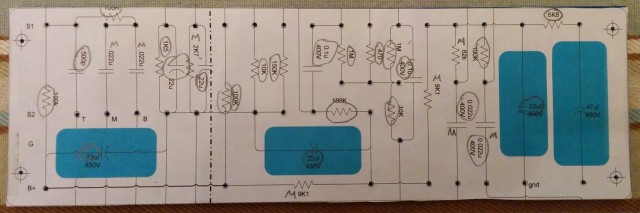
|
The full size template
for each board is printed and taped to the
board. I use a spring loaded center punch to
mark the location of each hole to be drilled.
My basic vertical and horizontal grid is 0.375"
(3/8"). I alter the grid where necessary to
accommodate larger components, like filter caps.
|
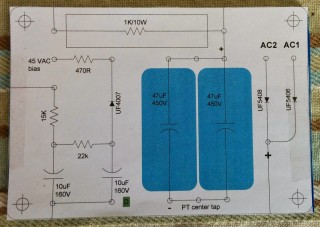
|
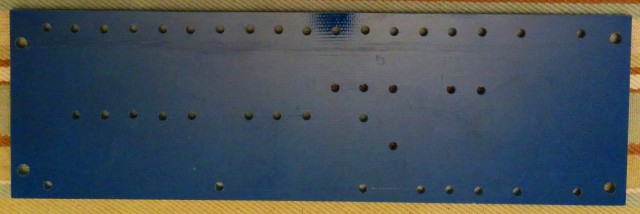
|
The main turret board is
8" x 2.5" constructed on 0.125" G10-FR4 glass-epoxy
(aka Garolite) from McMaster-Carr.
The power supply board is 4" x 2.75".
The drill size is #33 (0.113"), which is just 0.001"
larger than the turret body for a very snug
fit. It is critical to use the correct size
drill for the turrets
|
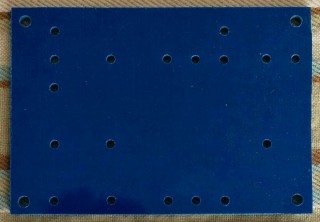
|
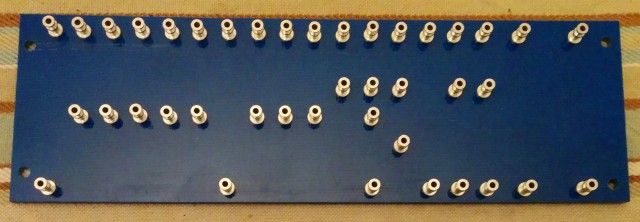
|
The Keystone turret
lugs are Mouser
Electronics part 534-1509-4. They are
now very expensive, ($0.25/per), even when ordered
in 1000 quantity.
I set the turrets on my drill press (not plugged in)
using the Keystone staking tool 534-TL-8, also
available from Mouser. The pointed
end of the Keystone tool has a complex profile that
flares every turret perfectly. It was worth an
$18 tool to not ruin any more turrets.
|
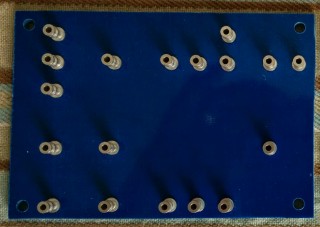
|
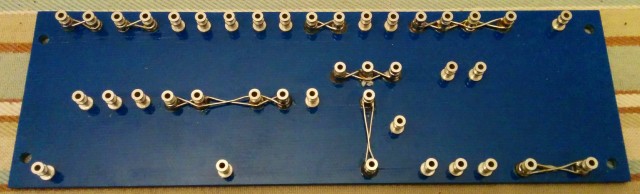
|
The appropriate turrets
are laced together with #22 soft tinned buss wire,
using Doug
Hoffman's technique. |
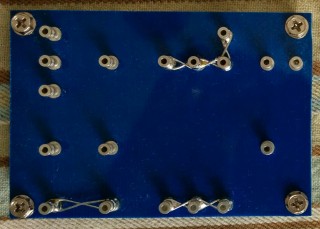
|
|
Front panel controls
The original front panel of the Peavey had plenty of holes
for the controls. I added a few more holes and resized
some others during the course of my original tube conversion
project. Needless to say, it was in a pretty ugly
state at the start of this project.
I had several blank 19" x
1.75" x 0.125" aluminum panels left over from my 1U rack
preamp projects. It turns out that the Peavey's front
panel was 1.75" high, so it was natural to hide the ugly
chassis panel with one of the aluminum blanks. Arpad
trimmed the rack ears off a panel blank, and drilled the
control holes on his Bridgeport mill. The front panel
cover brought two complications: the added thickness
of the aluminum panel over the steel chassis only left a few
threads exposed on the potentiometer bushings.
Fortunately, that was enough for the retaining nuts to
hold. The second problem was that the added thickness
pushed the chassis back from the mounting screw locations in
the combo cabinet. I could have trimmed an additional
3/4" from each end of the aluminum panel, so the panel would
not change the location of the chassis in the cabinet, but I
really liked the look of the full width cover. I
borrowed a 1/8" end mill from Arpad, chucked it in my hand
drill, and elongated the holes in the cabinet by 3 mm.
The beauty washers for the chassis mounting screws were
large enough to cover the elongated holes, so my quick hack
doesn't show.
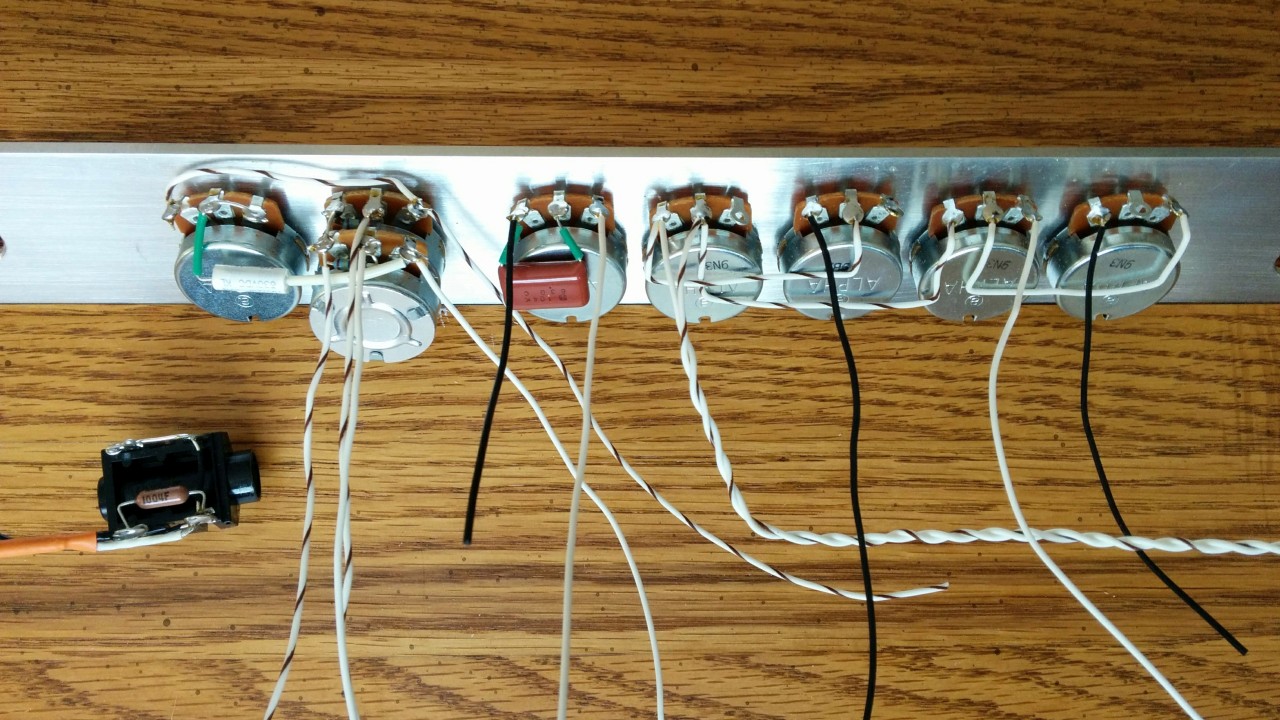
The aluminum front panel cover made a convenient way to wire
the front panel controls, mounted in their correct
positions, without having to do this inside the
chassis. That would have been a nightmare, because the
U-fold in the chassis makes the potentiometer terminals
nearly inaccessible. From left to right, the controls
are high cut, master volume, presence, bass, middle, treble,
and volume.
Jon, another co-worker of mine, arranged to get the front
panel anodized and laser engraved. I was going to make
another attempt to etch it myself using toner transfer and
copper sulfate solution, but I was happy to take the easy
way out. The standard non-hack way to obtain an
attractive front panel would have been to order a
laser-engraved or silk-screened beauty panel made from thin
aluminum, but I'm happy with the results obtained by using
materials I had on hand, and the generous contribution of
volunteer labor from of a couple friends.
|
Rear panel controls
The rear panel of the Peavey had some extra holes where I
didn't need them. I drilled new holes for the fuse
holder, speaker jack, and 6 bias voltage monitoring probe
jacks.
My output transformer only has 8 ohm output, so there is no
impedance selector. I'll eventually make a beauty
cover for the rear panel. For now, it's gonna keep
showing its Peavey tattoos.
The red probe jacks are, left to right, B+ at output
transformer center tap, and plate voltage for each 6V6
output tube. The upper jacks are 6V6 #2 cathode,
cathode ground, and 6V6 #1 cathode. I can thus set
output tube bias using either the cathodes or the plates.

|
Assembly and first power up test.
Things went together pretty well. The only part that
was difficult to wire is all the stuff by the rear
panel. Since this chassis is about an inch less deep
than the standard Trainwreck chassis, there is not much
space between the output tube sockets and the rear
panel. It also has less vertical space than a
typical tube amp chassis. Since I included 6 voltage
probe jacks for output tube anodes, cathodes, cathode
ground, and OT center cap, the area by the output tube
sockets and output jack is pretty crowded. I'm glad I
made an accurate scaled chassis layout in Visio. It
would have been less hairy if I were starting with a new
blank chassis, but my adaptation of the recycled chassis was
satisfactory.
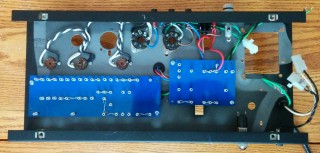
|
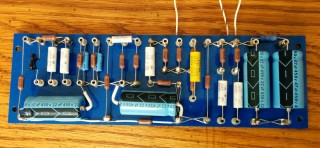
|
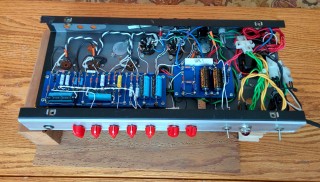
|
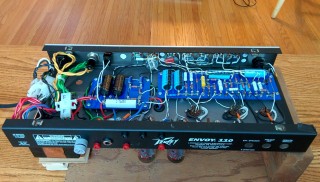
|
Filament and power tube wiring
complete. Checking circuit board fit.
|
Components inserted into main circuit
board. Many connections are soldered after the
board is mounted in the chassis.
|
Front view of assembled chassis on my
test stand
|
Rear view of assembled chassis on my
test stand.
|
For my own "experimental" builds, I don't trim the
transformer leads short for maximum neatness, as the
transformers may get moved to a different chassis
someday. So I braided them and secured them with nylon
wire ties.
After wiring everything, I verified that there was high
resistance between all power rails and ground, the low
resistance between all ground points. Then I began
power-up testing with a variable autotransformer (Variac),
with the tubes removed. During this process, I
discovered two problems: I forgot to ground the positive
side of the bias supply to the screen ground, and I forgot
the resistor between the bias pot and ground needed to scale
its voltage into the proper range. It was late, so I
shut down and went to bed. The next morning, I
corrected these problems and installed the tubes. I
set the bias for maximum negative voltage. With the
power and standby switches turned on, a guitar connected to
the input, and a speaker connected to the output, I slowly
brought up the voltage on the variac. After about
minute with no indications of trouble, I reached a B+
voltage of about 200 VDC, and the filaments were hot enough
for cathode emission. Beautiful clean tones emerged
from the speaker. It worked on the first try! I
continued slowly raising the mains voltage until it reached
120 VAC, and nothing bad happened. I did a quick check
of all the B+ node, plate, and cathode voltages: everything
looked good.
Setting the bias
I built in probe jacks to measure the voltage drop across 1
ohm resistors between the power tube cathodes and ground,
but I neglected to order said resistors with the other parts
for this build. No big deal. I just wired a
jumper between the cathode probe jacks and cathode
ground. I'll replace the jumpers with 1 ohm resistors
after my next parts order. Another good way to measure
idle plate current is to measure the DC resistance between
the output transformer primary center tap and each plate
lead. Of course one measures this resistance with the
power OFF. For my OT, a Weber
W041318, that was about 140 ohms per leg. Plate
current for each tube can then be calculated from the
voltage drop between the OT center tap and plate lead using
Ohm's law. So if I wanted to bias each 6V6 for 25 mA
plate current, I'd want to see V = I * R = 0.025A x 140 ohms
= -3.5 VDC between the OT CT and each plate lead. With
370 VDC on the plate, 25 mA gives 9.25 W idle plate
dissipation. The JJ 6V6-S's I'm using are specified
for 14W max dissipation, so my idle dissipation is about 67%
of max. This might be a bit hot for an Express with
heavily overdriven output tubes, but I don't expect to be
there much. At some point, I'll hook up a dummy load
and make sure I'm not red-plating in a darkened room when
I've got it cranked. In any case, when I adjusted the
bias pot to give me a 3.5 VDC drop from CT to plate, the
bias voltage was -31 VDC at a plate voltage of 370
VDC. This agrees well with the nominal curves shown on
the JJ's plate characteristics chart for this tube.
When using this OT voltage drop method to measure plate
current, it is important to let the tubes and the OT to warm
up, as the OT's resistance will drop as its temperature
rises. At some point, I intend to cross-check the
results among the three "good" bias measurement methods
(direct plate shunt current measurement being the third
method).
Sound check
With the bias set, it was time to check the sound. The
amp sounded pretty awesome, just like the sound and video
clips posted on YouTube, et. al. Everything from
shimmery clean to Van Halen grind is on tap, just by turning
the guitar's volume pot. The speaker in the combo
cabinet is a Weber Signature 10S Alnico, rated for
15W. I think it sounds very nice in this amp, smooth
with good balance everywhere. I'm slightly afraid that
this amp has the power to destroy it if I get too
enthusiastic. I also tried my EVM 12L (150W) in an
external cabinet, and that thing was monstrous, tight as a
drum with lows the Weber couldn't touch. That's not a
knock on the Weber, as those speakers are very different
animals. I also tried a budget Weber Signature 10
ceramic. That one was all midrange, and not enough
treble for the way I play.
It was a radio too, for a little while
I had an FM radio station coming out of the speakers
intermittently, so RF was getting in. During my
initial testing, I had no RF cap between the input jack ring
terminal and chassis ground, and no grid stopper resistor on
the input. I add the RF cap, and that took care of
most of it, but some was apparently coming in on the
instrument signal lead. I added a 20K grid stopper on
the input triode's grid pin, and the radio was gone. I
didn't notice any damage to the amp's "touch sensitivity",
or any additional treble loss with the guitar's volume knob
turned down.
No squeals or oscillation with everything dimed
I think I've got it all wired nice and tight, with no
unintended feedback between stages. I'm not quite sure
if the negative feedback (NFB) in the presence control is
ideal. I used a 100K resistor between the OT secondary
and the phase inverter tail, with a 25K presence pot instead
of the "correct" 5K pot. Another item for the next
parts order. With minimum NFB, the gain is pretty darn
high, and I can hear taps on the chassis and at least one
preamp tube pretty well. I may have to do something
about damping microphonic tendencies in the preamp tubes.
I looked for oscillations everywhere with my oscilloscope,
and didn't see any. Nor did I hear any weird
intermodulation tones while playing the guitar.
Master volume and high cut control
The master volume and high cut controls work well together.
The tone can get fizzy when the master volume is turned down
a lot, and distortion is coming from the preamp. The
high cut control really fixes this up, and eliminates the
need for the (typically 47 pF) "fizz" cap between the phase
inverter outputs. If you're going to build an Express
with a master volume, I recommend including the high cut
control as well. It's also handy for tweaking the high
end behavior for different guitars, volume control position,
pickups, or speaker cabinets.
Guitar wants treble bypass caps
Playing a Trainwreck clean means the guitar volume control
is going to be rolled back a lot, which usually means the
guitar's treble response will also be progressively
reduced. Pre-Wreck, I rarely used the guitar volume
control, mainly because the sound did get dull. Time
to research options for installing treble bypass caps on the
volume controls of my guitars. My everyday guitar is a
1975 Les Paul Standard with Bill Lawrence (rip) L-450's with
push-pull coil splits on the tone pots. It sounds
great on every pickup in both single coil and humbucking
mode.
Guitar volume and tone controls changed from "modern" to
50's style
Instead of adding a treble bypass cap and resistor to the
volume control, I ended up re-wiring the Les Paul's controls
from modern
to 50's style. Now the treble doesn't roll off
as the volume is rolled back. The taper and
interaction of the volume and tone controls also changes
significantly, so I had to re-learn how to use the
controls. Looking at a bunch of guitar forum posts,
there are many possible ways to tweak the volume and tone
controls. The straightforward conversion from modern
to 50's style was good enough for me.
Conclusion
Building my first Trainwreck was a satisfying experience,
and produced a very playable amp. I like it so much,
it's getting a finished front panel. It think it
delivers the Trainwreck sound (as much as I can know what
that is from sound clips), even with the inexpensive PT and
OT I had on hand. I think it would be worthy to invest
in the "correct" iron and chassis for my next build.
I'm happy with my original circuit board layout - I can
think of a few tweaks I might try to incorporate in future
builds, but I did not find any significant problems with my
first attempt.
|